24 FEB. 2025
From process development to industrial manufacturing of biomolecules
Development of cell culture and Purification processes
In order to quickly obtain a high-quality product that remains competitive on the market, the process developed must be transposable transposable to industrial scale. To meet this important challenge for its many start-ups and biotech company partners, LFB BIOMANUFACTURING uses cell lines specially adapted to serum-free / protein-free media and optimised to increase yields.
We develop the cell culture (Upstream process = USP) and purification (Downstream process = DSP) processes in state-of-the-art facilities. Our USP/DSP development workshops work with both Ambr® 15 and Ambr® 250 microbioreactor systems and single-use bioreactors (ranging from 3 L to 50 L) as well as all associated capture and purification systems in order to generate material and ensure successful passage to industrial scale (or “scale-up”).
Example of industrialisation complex molecules
LFB BIOMANUFACTURING’s specialists team up with the LFB Group‘s network of experts to facilitate the development of optimal cell culture conditions for each line. Our engineering teams also have extensive experience in selecting the most suitable chromatography and filtration processes and associated viral elimination methods, taking into account the complexity of the molecules and any need for custom development.
Thus, LFB BIOMANUFACTURING has successfully developed scores of complex processes and is now able to produce a large number of therapeutic proteins at industrial scale.
The classic manufacturing process resulting from development of the cell line and USP/DSP processes as well as the associated analytical development stage includes the manufacturing of 50 L batches (non-cGMP feasibility batch, batches for toxicology tests, etc.) in a pilot zone and the scale-up to 2,000 L in one of its 3 multi-product cGMP production zones.
The experience acquired by LFB BIOMANUFACTURING over the last 25 years, as well as its well-established development platform, allow it to adapt to any type of process and to scale up to 2000 L without impacting cell viability or yields, as illustrated by the example scale-up (50 L to 2,000 L) carried out in the framework of the production of a monoclonal antibody (DG44 line).
Therefore, LFB BIOMANUFACTURING, a pioneer in single-use technology, has developed unrivalled expertise in the use of single-use bioreactors and, as a result, is not constrained by the technological differences between different equipment manufacturers, and technological changes have no influence on the successful scale-up of processes to industrial scale.
Nevertheless, beyond the reference scale (2,000 L), a scale-out (use of multiple 2,000 L) rather than an additional scale-up is proposed, in order to de-risk production (production volume, product quality and process development already established at the 2,000 L scale), reduce costs (no development at a higher scale) and stick to deadlines for the completion of clinical and commercial batches (an unforeseen event in one bioreactor has no impact on the production as a whole).
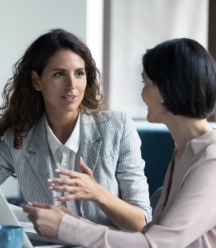